Learn how Voxel's solutions help reduce risks and streamline processes across industries such as Food & Beverage, Logistics & Supply, and Manufacturing. Voxel enables businesses to enhance safety standards, minimize liabilities, and boost productivity, ultimately fostering customer loyalty and sustained growth.
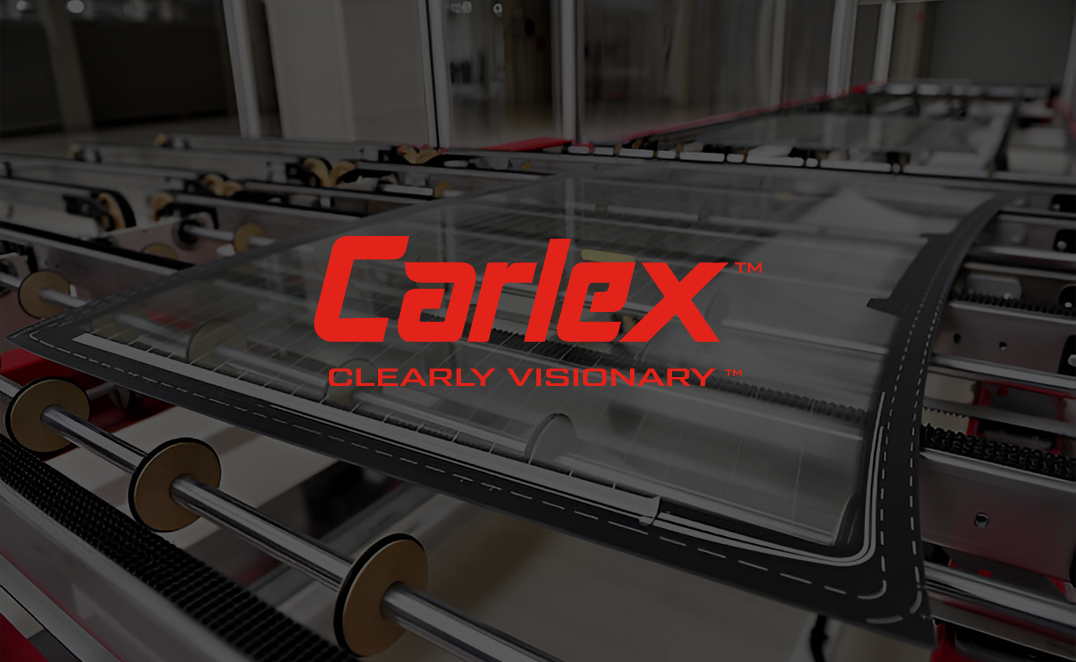
Carlex Glass Creates a Positive Safety Culture and Safer Workplace with Voxel
In under 3 months, Carlex Glass reduced the risk of forklift incidents and improved PPE compliance while continuing to build their safety culture with compassionate data-based leadership.
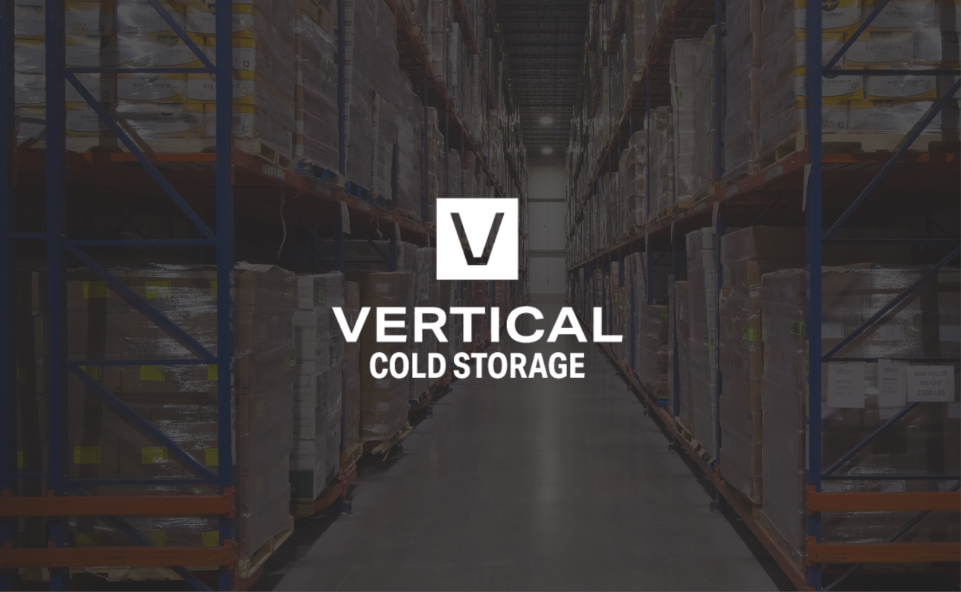
Vertical Cold Storage Revolutionized Workplace Safety Amidst Rapid Growth
With Voxel, a dramatic reduction in ergonomic and vehicle-related risks also resulted in fewer injuries, lower turnover, and lower maintenance costs.
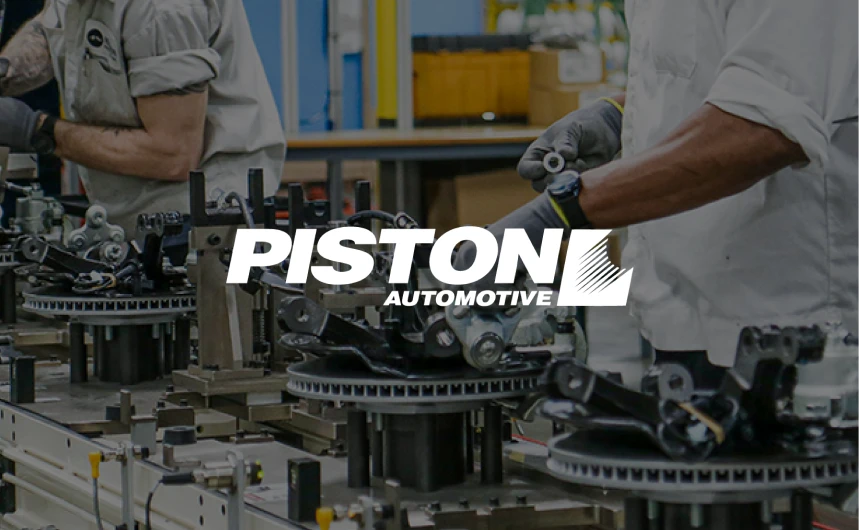
Piston Automotive Boosted Manufacturing Plant Safety with Voxel
Piston Automotive boosted safety and efficiency at Marion, OH facility, reducing forklift incidents by 86% and advancing a proactive safety culture in 3 months.
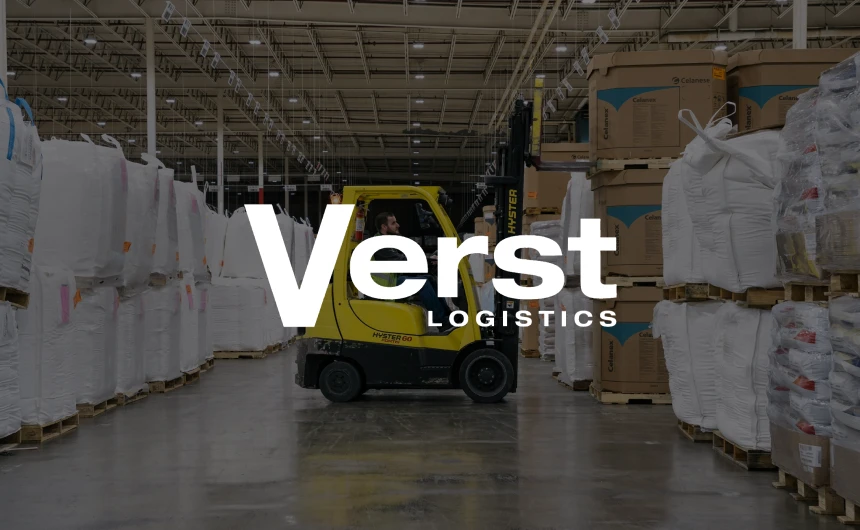
Verst Logistics Cut Vehicle and Ergonomic Incidents in Under 6 Months
Leading 3PL provider enhanced warehouse safety and efficiency with Voxel, reducing vehicle and ergonomic incidents by 82% and 50%, respectively, in 5 months.
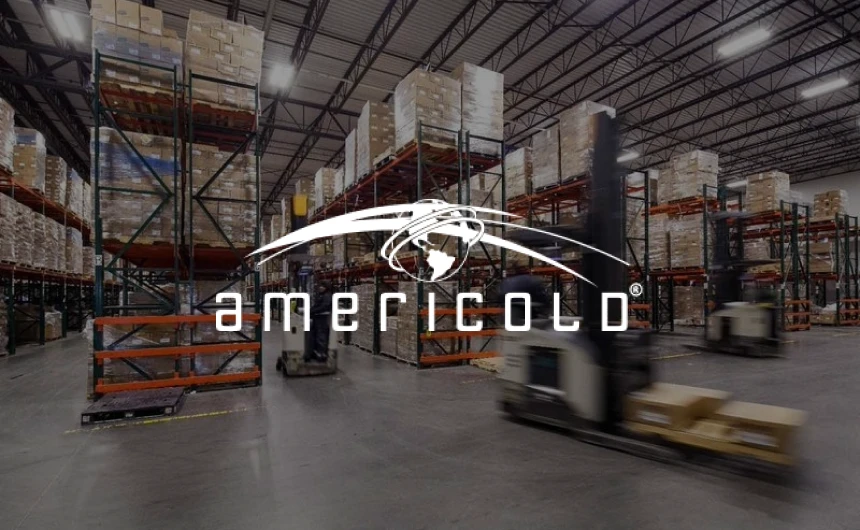
Americold Saved $1.1M Annually and Reduced Injures By 77%
Americold Logistics, a Fortune 500 cold storage provider, transformed its safety and operational landscape within 12 months using Voxel's safety intelligence platform.