The ROI of Safety
Team Voxel
January 16, 2024Determine the ROI of your safety programs and see how you can improve the bottom line by increasing productivity and decreasing risk and injury.
Measuring the ROI of safety is a challenge. Most organizations settle for tracking reactive metrics like number of incidents, insurance premiums paid or workman's compensation claims, but that only tells part of the story.
In this article, we'll show you how to get a complete picture of the ROI of your safety programs by taking a more proactive approach. You'll learn how getting better visibility into everything from ergonomics to vehicle safety and PPE practices helps you understand, and respond to, the needs of your organization.
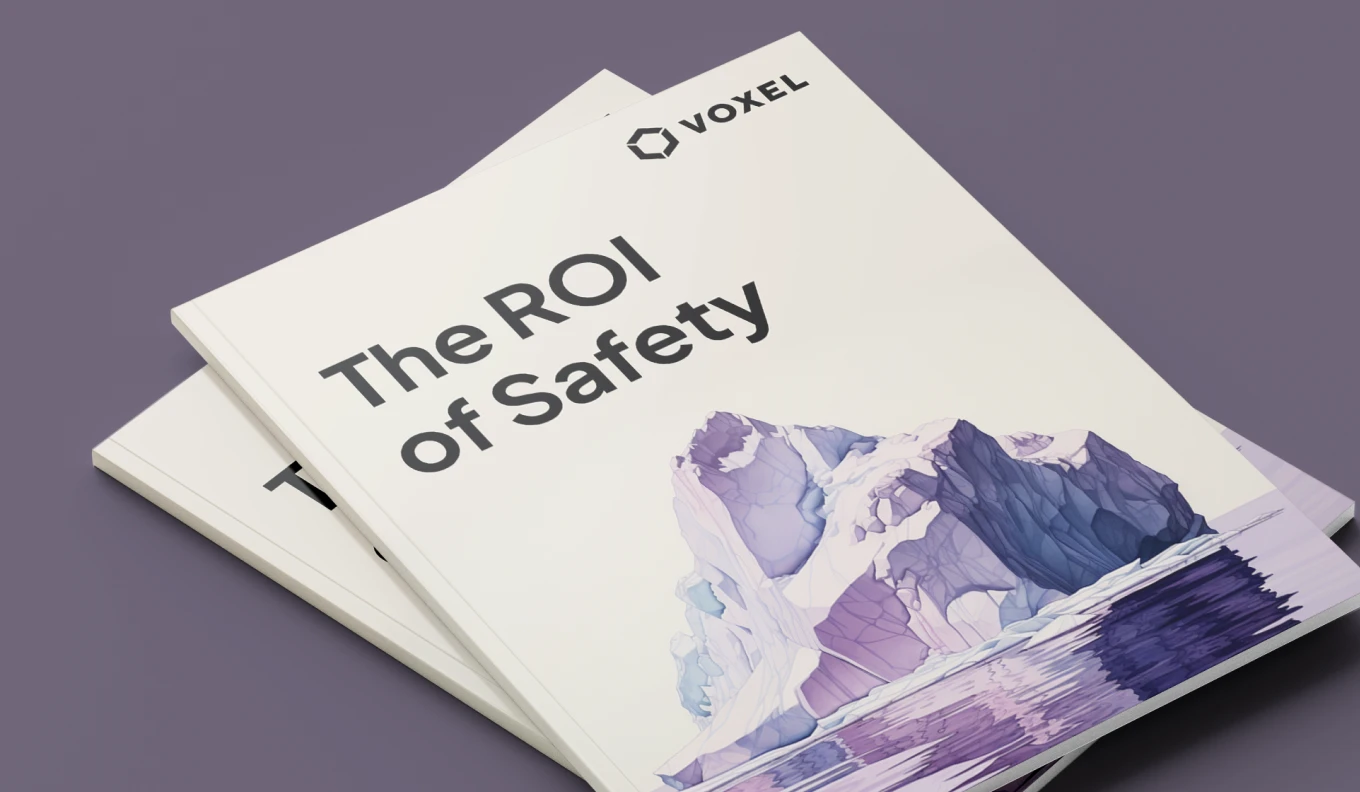
Risk and Safety leaders know that the benefits of a safety program often speak for themselves. We choose initiatives based on their potential to help get our employees home safe on a daily basis, and minimize long-term stress and injury.
But what happens when we need to communicate the value of those initiatives to other teams? How do we tell a CFO, for example, why we should invest in technology and programs that keep our employees safer? That’s when it’s important to put safety in terms that everyone understands: return on investment (ROI). For example, an automobile tire retailer replaced 50-cent pairs of gloves with a more expensive (and safer) brand, driving its annual glove costs up by $200,000—but the reduction in injuries saved more than $1 million of losses. Minor adjustments in safety policy have major results.
In this post we’ll explain the current challenges around measuring the ROI of safety and how you can overcome them.
Measuring the ROI of Safety is Challenging
Measuring the ROI of your safety programs is challenging for a few main reasons:
- Safety programs are far-reaching, touching everything from PPE to ergonomics to vehicle safety
- It’s challenging to get visibility into the day-to-day implementation of safety procedures and training
- Most organizations are only able to track losses when an incident happens, but they’re not able to accurately track when a loss is avoided
Safety intelligence today has often relied on anecdotal feedback from the sites themselves at best and reactive measurements like injuries, incidents and losses in paid insurance premiums and productivity. As a result, safety programs are often judged by how well they help organizations decrease those costs.
However, just measuring injuries, paid insurance premiums and lost productivity makes it so you’re missing most of the safety picture. You don’t get insight into why those injuries are happening, what happened upstream that could have been avoided, and how you can enact policies, procedures and training that help keep everyone safe.
Overcoming Those Challenges is Critical
The fact remains that an improved safety record can substantially reduce insurance premiums and indemnities, slashing a major direct cost of injury. But OSHA estimates that the majority of the costs of injury are indirect, uninsured, and unrecoverable.
According to OSHA’s injury cost calculator, a machine crushing accident costs, on average, $57,000 in direct losses and $62,000 in indirect costs. A 2011 study at UC Davis Medical School showed that indirect costs are typically 2.7x greater than direct medical costs: if an average back injury has a direct medical cost of $25,000, the “real” cost of the injury may be closer to $90,000 or more. Depending on your profit margins, your business may require millions of dollars of additional sales to make up the difference.
According to OSHA’s injury cost calculator, a machine crushing accident costs, on average, $57,000 in direct losses and $62,000 in indirect costs.
The enormous indirect costs of injuries creates proportionally large returns on safety. A cultural emphasis on safety is a unifying point between employers and workers, who both benefit from a safe working environment. Improved worker morale results in increased productivity from a collective buy-in to your company’s mission. And long-term worker retention generates compounded cost savings from low turnover: keeping your veteran employees reduces the costs of recruiting and training new employees, and avoids paying inflated wages to compete for scarce workers in a tight labor market.
We’ll focus this analysis on safety intelligence programs – a term used to describe anything that gives you more insight into the day-to-day safety of your organization and provides you with proactive feedback that helps prevent incidents. Better insights into how safe your sites are gives you concrete data that can lead to a better understanding of the ROI of your efforts as well as a better idea of which efforts to choose for the most impact.
The Challenges With Safety Intelligence Today
In order to establish the ROI of a safety intelligence program, let’s look at how safety intelligence and insight is usually gathered. In a typical safety program, an EHS consultant does an audit and a site manager implements their recommendations. This intervention is usually reactive – it begins after an adverse event has already taken place. After their initial analysis, most EHS programs use generic guidelines that claim to help you shore up gaps in your safety strategy. These might be recommended changes to your employee’s process, but they might also be training seminars on recommended topics.
The problem with this approach is that by definition, you’ve already experienced obvious losses in workers compensation and insurance premiums as well as the hidden costs like low morale, time spent on paperwork and lost productivity.
In addition, reactive safety intelligence produces inconsistent and short-lived results. A human observer walking around for a few days with a clipboard cannot holistically evaluate your environment, and the changes they recommend are often not tailored to your organization. There’s very little ongoing follow-up which means that there’s no insight into how those changes are impacting your overall safety culture, and no effort to optimize the strategy for maximum long-term impact.
Reactive Training is Ineffective
The main response to many of the identified gaps is to double down on training. Unfortunately, a recent survey of American businesses by Intertek found that 1 out of 3 companies is unable to verify if their safety training is effective. More than half of respondents reported that their workers didn’t improve safety compliance after training. Some companies have tried to hire more training staff, adding additional labor costs in an already tight labor market. In 2021, training payroll reached $69 billion, a nearly 30% increase over pre-pandemic levels. Training expenses continue to rise annually, and with no clear impact to the bottom line.
Unfortunately, a recent survey of American businesses by Intertek found that 1 out of 3 companies is unable to verify if their safety training is effective.
Training itself isn’t the problem, but the way that training is applied today isn’t effective. Most of these trainings are ineffective because they’re not tied to actual areas of improvement for each individual site, and because there's no follow-up and ongoing measurement to ensure accountability.
The Solution: Proactive Insights That Drive Immediate Action
Instead of reactive assessment followed by ineffective training, the solution is to implement a proactive strategy that not only provides peace of mind but also helps improve productivity and decreases losses from safety incidents in the short and long term. In order to get there, you need two things: visibility and strategies based on data.
Visibility: Get Always-On Insight
This first step is to improve your visibility. You need to have a complete picture of what’s happening on a daily basis so that you can measure how closely your safety procedures are followed, and take action immediately when they’re not. In order to avoid incidents before they arise, you need real-time insight into things like:
- Ergonomics assessments
- Environmental hazards
- Vehicle safety
- PPE usage
You need to be able to see these things, measure how often your policies and best practices are followed and understand how the failure to follow these could be leading to an increase in injuries, workers compensation claims and lost productivity.
Voxel helps you do this by turning your existing security cameras into a safety intelligence program that analyzes all of your footage in real-time using an AI engine that’s programmed to watch for everything from biomechanical errors like improper lifting to vehicle safety concerns, spills, blocked exits and even PPE use. We’ll work with you to implement tracking for best practices like research from Stanford’s biomechanics lab for ergonomics, and we’ll also customize your tracking to focus on areas and policies that are important to you.
Artificial intelligence adapts to the needs of specific worksites, by targeting safety factors that impose the highest costs. A 2016 study showed programs to prevent musculoskeletal injury generate an average of 350% returns; other studies suggest more than 10:1 returns on ergonomic safety. The most common and costly machine injuries, such as crushing and entanglement, are easily avoided through proper use of machine safeguards and personal protective gear (PPE).
Data-Focused Safety Strategies
After you’ve improved your visibility, you need those insights to be compiled in aggregate in order to help you identify things that need your immediate attention, trends that need to be prioritized in your longer term strategy and areas where your team is doing well.
With Voxel, all of these insights are then compiled into a dashboard that shows you how safe your sites really are. That way, you’re not just plugging in vague, reactive training, you’re actually able to customize your response to actual day-to-day issues that make life better, safer and more productive for everyone.
Voxel’s automatic “triage” system flags high-priority incidents and sends your team a daily report of action items to help create teachable moments. Research shows that using site-specific videos doubles employee engagement with safety training. An operations manager can bring recommendations back to their team while the memory of an incident is still fresh: like a basketball team reviewing film after a game, video intelligence creates a culture of incremental improvement and attention to detail.
Example: Americold Logistics Reduced Injuries by 77%
Take Americold Logistics for example. They already understood that creating a safe worksite requires a continuous commitment to improving safety culture and norms. In 2021, cold storage provider Americold Logistics achieved a 77% reduction in injuries in less than one year at their distribution center in Modesto, California. In addition to safety-related savings, Americold also used Voxel to mitigate a major inefficiency in their operation, tracking open doors to reduce energy costs in a temperature-controlled warehouse. The result was a direct annual savings of $1.1 million at a single warehouse site: a 2,000% direct return on their investment, before factoring the numerous indirect costs of injuries.
The result was a direct annual savings of $1.1 million at a single warehouse site: a 2,000% direct return on their investment, before factoring the numerous indirect costs of injuries.
What’s the ROI of Your Safety Program?
As you consider the ROI of your own safety intelligence program, here are some questions to consider:
- What are the direct and indirect costs of injuries in your organization?
- How much does your organization spend on EHS consultants?
- How much time, money and effort is spent on safety training?
At Voxel, we know that ensuring the safety of your employees is a heavy responsibility. Our technology makes it so that you feel confident that everyone, everyday returns home unharmed.